变形区
- 网络Deformation zone;flexing area
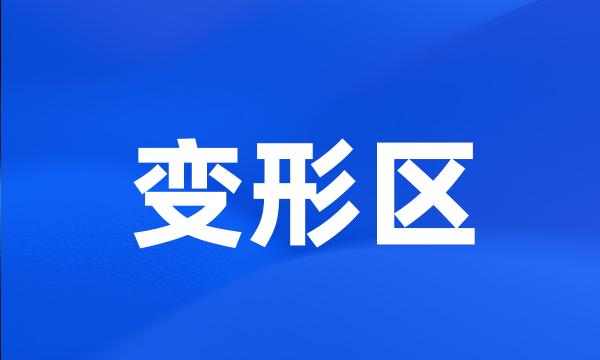
-
第一切削变形区中SiC增强相的重定向研究
Research on the Reorientation of SiC Reinforcements in the First Cutting Deformation Zone
-
压痕诱发GaAs塑性变形区的层错结构
Stacking-fault structure induced by indentation in GaAs
-
AccuRoll轧管机变形区空间横截面的计算机模拟
Computer simulation of deformation zone space cross section of ACCU-ROLL pipe mill
-
由于PC热连轧机轧辊成对交叉,因而在变形区接触表面产生随交叉角变化的轴向力。
A changing axial force generated on the contacting surface of deforming zone results from the change in the cross angle of rolls during strip hot rolling .
-
利用有限元软件模拟了V型砧的锻造拔长过程,并对不同夹角的V型砧压下后锻坯塑性变形区内应力、应变的状态进行比较。
The V-anvil drawing process of large forgings was simulated using FE software , and the stress-strain distributions in the plastically deforming area were compared after different V-anvils drawings .
-
特征距离与裂纹尖端钝化所产生的有效变形区尺寸(2c)相对应。
The characteristic distance corresponds to the extent of effective deformed region ( 2c ) resulted from blunting of crack tip .
-
当r1,自由变形区的卷曲半径大于模具圆角半径;
When r 1 , and the radius of the free deformation zone is larger than that of fillet die ;
-
用计算机模拟送进角与辗轧角对Accu-Roll轧机变形区的影响
Influence on Deformation Zone by Feed Angle and Toe Angle Using Computer Simulation
-
最后,通过Taylor碰撞算例验证了本文塑性程序的有效性,并对弹丸撞击飞机加强蒙皮实验进行了数值模拟,研究了变形区直径、变形区深度和弹丸剩余速度与弹丸初速度的关系。
Finally , the plastic program is proved to be correct and efficient by Taylor impact . In addition , numerical simulation for impact of bullet on airplane skin is carried out .
-
以4200mm轧机轧制71块钢板的实测数据为基础,利用Matlab人工神经网络工具箱,建立了轧制变形区的应力状态系数的RBF神经网络预测模型。
Based on the experimental data obtained from 71 steel plates rolled in 4200 rolling mill , this paper established a RBF neural network prediction model of influential coefficient in stressed state by Matlab neural network toolbox .
-
并提出断裂韧性与缺口韧性、拉伸塑性的关系取决于尖裂纹前沿有效变形区尺寸(2c)与原奥氏体晶粒尺寸(dγ)的相对大小。
The relationship between fracture toughness and notch toughness 、 tensile ductility depends on the relative size of effective influence region ( 2c ) and austenite grain .
-
使用光学显微镜、显微硬度计、X射线衍射、SEM、TEM等方法对高速切削30CrNi3MoV高强度钢锯齿形切屑中第一和第二变形区内形成绝热剪切带和白层进行了观察和研究。
Adiabatic shear bands and white layers in primary and secondary deformation zones within the serrated chips formed during high speed cutting of 30CrNi_3MoV steel were investigated by optical microscope , microhardness tester , XRD , SEM and TEM .
-
结果表明,异步轧制单位压力分布仍具有峰值;搓轧区占变形区比例x越大,异步轧制的降压效果和摩擦峰的削减作用越大;
It was found that the frictional peak in the specific pressure distribution still exists under asynchronous rolling , the larger the x ( ratio of cross-shear zone to deformation zone ), the greater the effectiveness of reduction in pressure and frictional peak hight .
-
对焊缝区、变形区及热影响区的金相组织分析结果表明,淬火45钢LFW过程中,焊件不同部位的显微组织随着回火温度的变化而相应变化。
The microstructure observation showed various structures were evolved at different regions of joint , which corresponds to different temper temperatures during LFW .
-
Marc软件,采用弹塑-热耦合有限元方法模拟出刀具在切削7075薄壁件过程中各变形区内温度、应力、应变以及切削力的分布。
Marc software and elas-plas-thermal coupled finite element method are used to simulate the distribution of temperature , stress , strain and cutting force in different deformation areas in cutting process of 7075 Al alloy thin-wall workpiece .
-
通过比较流体润滑状态下冷轧变形区摩擦系数与轧机允许最小摩擦系数得出轧制稳定因子KS,用于判断其轧制过程是否稳定。
The stable rolling factor K S was developed to decide the stability of rolling process by comparing the friction coefficient in hydrodynamic lubrication rolling with allowed minimum friction coefficient in rolling .
-
设计了基于数字信号处理器DSP的热连轧自动厚度控制(AGC)实时仿真器,建立了调厚过程压下系统和变形区的动态模型。
A real-time simulator of Automatic Gauge Control ( AGC ) for hot-rolling mill based on Digital Signal Processors ( DSP ) was proposed . The models of the hydraulic cylinder for Automatic Position Control ( APC ) and the deformation area of each stand were built .
-
根据正交实验结果,提出了改善深井巷道围岩体稳定性的措施。经观测发现,煤柱分为3个区:塑性变形区,煤壁内0~4m;
According to the observation , it is found that the pillar can be classified as 3 zones in stress conditions as follows : ( 1 ) the plastic zone , 0-4 m from the edge of the pillar ;
-
通过对AccuRoll轧管机变形区中金属变形的理论分析和试验研究,探讨了轧制工艺特征和工具对轧制变形的影响。
And the in - fluence on workpiece deformation by the rolling process characteristics and the process tools is discussed on the basis of the theoretic analysis concerning the metal deformation in Accu-roll mill deformation zone and related ex - perimental research .
-
在建立Accu-Roll轧机变形区模型的基础上,开发出计算机模拟软件,可方便地通过变形区纵剖面计算机图象显示分析工艺参数对变形区的影响,从而为合理地选取与优化工艺参数提供依据。
Computer software for simulating vertical section of deformation zone on Accu Roll rolling process developed on the basis of models built , which puts the base for optimizing process parameters .
-
同时指出ECAE挤压过程中试样所受的应力场的不同,稳定变形区流动速率的不同和摩擦是形成变形不均匀的三个主要因素。
We also obtain that the different stress field , the variable flow velocity of steady deformation zone and the friction force are the main three factors resulting in non-uniformity .
-
本文按Ritz法求解最小能量方程,确定在直线及圆弧侧壁圆孔型中轧管时,变形区内金属的三维位移和应变函数。
Both three dimensional displacement and the strain function of metal in the deformation zone of continuous tube rolling under the condition of straight line and circular arc side wall pass were confirmed by Ritz 's method to solve the minimum energy equation .
-
1台体积为50m3低压搪瓷泄料槽筒体和封头连接部位,由于搪瓷化过程产生非自由热变形区,对其应力状况进行了分析测试。
The stresses at the non free thermal deformation zone of a 50 m 3 enamel vessel were tested . The deformation occurs in the joints of the shell and the head .
-
结合具体算例,用ADINA软件模拟了变形区的应力、应变及模具上的受力,得出了与理论分析相同的结论,即翻边使变形区变薄;
Using concrete calculated example , the stress , strain and the mold stress are simulated with ADINA software . It is shown that the simulation results of the stress strain change rule along with the die angle are in good accordance with that of the main stress method .
-
给出了角变形区变形特点,和球壳结构与角变形限量间的数值关系,经实践证明可同JB1127-82规定对应使用。
The numerical expression of quantity relations between the limit capacity of angle deformation and the structure of spherical shell have got , tests show that it may be used with JB1127-82 standard .
-
选择考虑冷轧带钢轧制过程变形区金属塑性变形和入、出口弹性变形的Bland-Ford-Hill模型作为冷轧过程控制轧制力模型并进行分析,确定出变形抗力和摩擦系数是影响轧制力最主要的两个因素。
The Bland-Ford-Hill model was used for rolling force calculation of process control of cold rolling . The plastic deformation in bite zone and elastic deformation at the entry and exit of bite zone were considered for the model calculation .
-
空间接触曲线和变形区模型方程的解析
Solution of spatial contact curve and model equation for deformation area
-
异步轧制时的特征角与变形区长度的计算公式
Formula for characteristic angle and asynchronous region length of asynchronous rolling
-
内孔翻边时变形区应力应变规律研究
Stress strain rule studies of deformation area of inside hole flange
-
轧制变形区油膜厚度的实验研究
Study on the Film Thickness of the Deformation Zone in Rolling